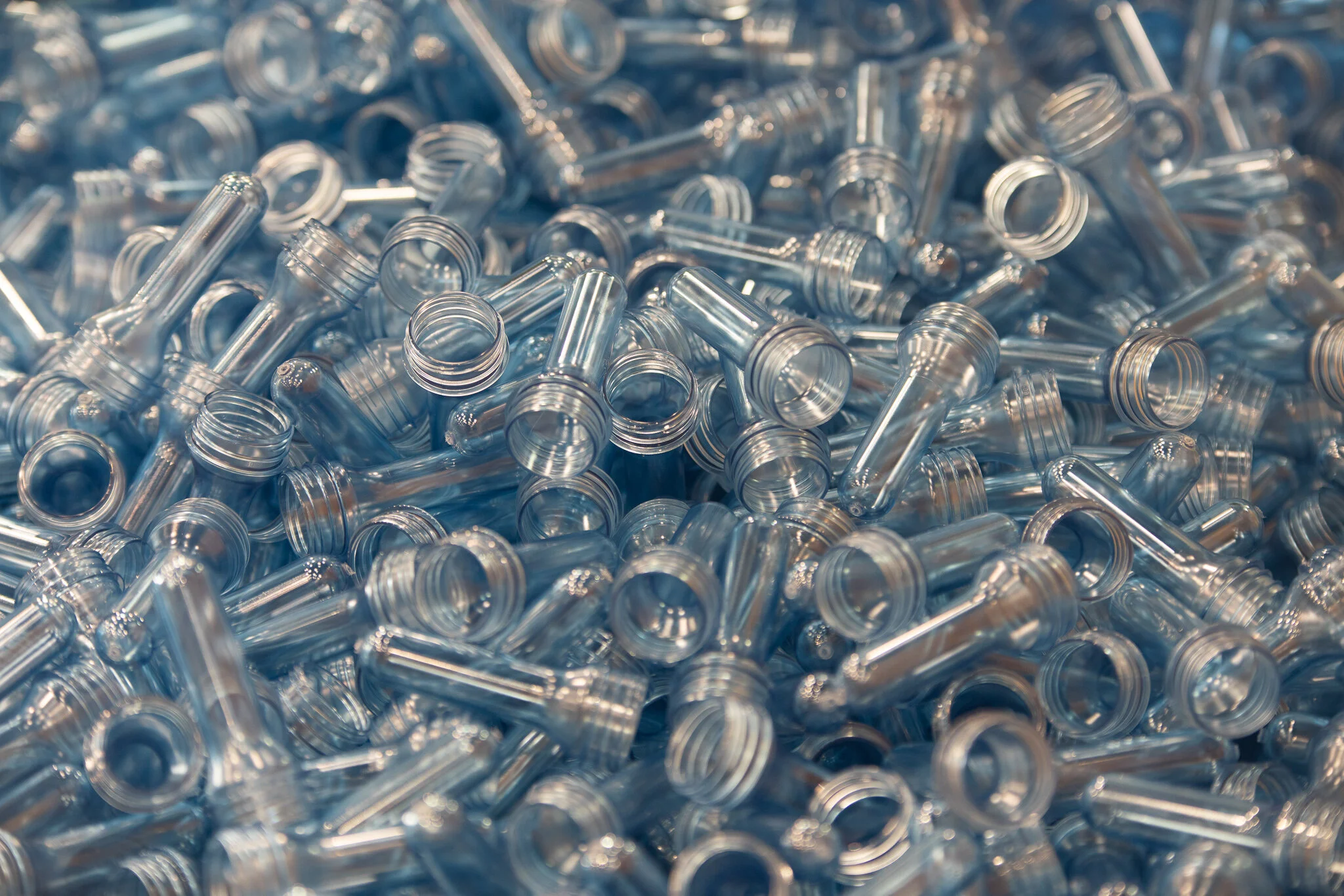
We Help To Elevate Your Business To Next Level
The Best Multipurpose Template in Market
Our Products
PET Preforms and Bottles
PET preforms are injection molded plastic pieces that are fed into blow molding machines to manufacture drinks and personal care bottles and containers.
PET preforms are polymers in a vial shape that are sold to bottlers, who feed them into their blow molding machines to produce bottles for water, juices and other beverages, as well as home and personal care products
Injection molding is the process for producing preforms. The process is ideal for producing high volumes of uniform products such as PET preforms for the blow molding of bottles.
PET is injected as a hot resin into a mold. The resin is fed into a heated barrel, mixed, and forced into the mold cavity, where it cools and hardens to the configuration of the cavity
HDPE Bottles and Containers
Blow molding is used by Takween to manufacture white and natural polyethylene and clear bottles (discussed above) ranging from 200 ml to 20 liters in capacity. The bottles are used in the dairies and beverages industries and thus require high quality products. HDPE and PP bottles compete with PET.
The blow molding process has essentially two stages in one process. In the first stage a preform of the hot plastic resin is formed with a hole in one end to pass compressed air through. In the second stage the compressed air expands the hot preform and presses it against a mold cavity. The pressure is held until the plastic cools – say, for 6 to 8 seconds. The mold then opens up and ejects the cooled, hardened plastic.
The three main types of blow molding are extrusion, injection and stretch blow molding. The extrusion process is widely used in the drinks and beverages industry. In extrusion blow molding there are continuous and the intermittent process technologies. The injected molded process is only used for small capacity bottles and is more difficult to control than extrusion as the plastic material is injected onto a core pin for subsequent blow molding rather than extruded into a hollow tube in the extrusion process. The stretch blow molding process first involves injection molding of preforms and then blow molding and can produce high volumes with limited restrictions on bottle design.
Flexible Packaging
The extrusion process is used to manufacture plastic film and sheet. The resin is pushed or drawn through a die of a predetermined thickness or cross-section. The main advantages of this process over other processes are its high volume, an ability to create very complex cross-sections and to shape materials that are brittle (because the material only encounters compressive and shear stresses).
Takween uses extrusion to manufacture polystyrene sheet rolls that are subsequently thermoformed into cups and lids in a single process. This is a high volume manufacturing process where the plastic raw material is melted and formed into a continuous sheet (or profile) and then cooled through a set of rolls that determine the sheet’s thickness and surface texture. The sheets are then sent for thermoforming.
Caps and Closures
Injection molding machines manufacture the caps and closures sold by Takween for use by the mineral water, soft drinks, juices, dairy and food industry. The resin is pushed or drawn through a die (mold) of a predetermined thickness or cross-section. The main advantages of the injection molding process over other processes are its high volume, an ability to create very complex cross-sections and to shape materials that are brittle (because the material only encounters compressive and shear stresses).
Thin walled Containers Thermoforming
Takween uses the thermoforming process to manufacture disposable white, semitransparent and transparent polystyrene cups and lids for the beverages industry with a rim diameter varying from 73 to 116 mm.
Thermoforming is a manufacturing process where a plastic sheet is heated to a pliable temperature, formed to a specific shape in a mold, and trimmed to create the desired product. The sheet, or “film”, is heated in an oven to a temperature that allows it to be stretched into or onto a mold and cooled to a finished shape. An integral part of the thermoforming process is the tooling which is specific to each part that is to be produced.
In comparison with injection molding and blow molding, thermoforming differs in that it is primarily used to manufacture disposable cups, containers, lids, trays, blisters, clamshells, and other products for the beverages, food, medical, and general retail industries. Thick-gauge thermoforming includes parts as diverse as vehicle door and dash panels, refrigerator liners, utility vehicle beds, and plastic pallets, but these are often injection molded in large volumes.
The conventional advantages of thermoformed thin wall and in-mold label containers are their lower capital and 75 operating costs and rapid mold cycles (production rate). The disadvantages are higher wastage, limited part shapes, and internal stresses that are common due to inherent wall thickness variation.
Drums, Crate and Pallets Plastic crates and pallets
The injection molding process is used to manufacture a wide range of industrial crates, pallets, pails, buckets, plastic plates, cups and utensils, tables and chairs, and the like.
High-impact resin (such as HDPE or polypropylene) and high-pressure injection molding technology enable the manufacture of more sophisticated designs. Wall thickness (thinner) and rib structure (thicker) of optimized to produce a platform that is lighter, stronger, with superior durability compared to other molding methods and materials
Plastic Drums:
As in food and beverage bottles production, blow molding is used to manufacture water, chemical and oil drums, jerry cans and other large containers. HDPE is typically the polymer used for drums; but polypropylene and other polymers may also be used
Large drums of up to 55 gallons are used for the food service, chemicals and oil products industries
Nonwoven Fabrics
The term “nonwovens” is used to describe a range of technologies making textile products in ways other than the traditional weaving and knitting methods. The technology used by SAAF is polypropylene spunbond and spunmelt, which is the most common of the nonwovens technology due to its relatively low cost of manufacturing Spunbond and spunmelt is a method of extruding polymer and turning it straight into a fabric in one process, without going through the steps of making fibers, yarns etc. This is a hybrid of textile and papermaking technology. In simple terms the molten polymer is extruded through fine holes and then, as it cools, it is stretched by the use of air jets to make controlled diameter filaments. The filaments are laid, as randomly as possible in all directions, on to a belt running the length of the machine. This process is repeated at each beam of the machine so a multi-layer product is produced. At the end of the process these layers are bonded together by the application of heat and pressure to form one coherent fabric. The spunbond (S) beams are on the front and back of the machine so S is on the outside of the product as these S layers supply the strength and wear characteristics of the final fabric. The meltblown (M) layers are sandwiched inside the S layers and control the water and air permeability of the final product. In a surgical gown, for instance, the requirement is for air to pass through for comfort but a high level of barrier to fluids to be in place to protect the surgeon from any body fluids reaching his skin during the operation.
Demand for polypropylene spunbonded and spunmelt nonwoven products originate from consumer, medical or industrial applications. Medical end-products include gowns, drapes and sterile wraps. Non-medical uses of nonwoven fabrics are generally found in construction, automotive, home furnishings and packaging segments within the industrial sector with the Hygiene sector (babies’ products, feminine care etc.) being the biggest market